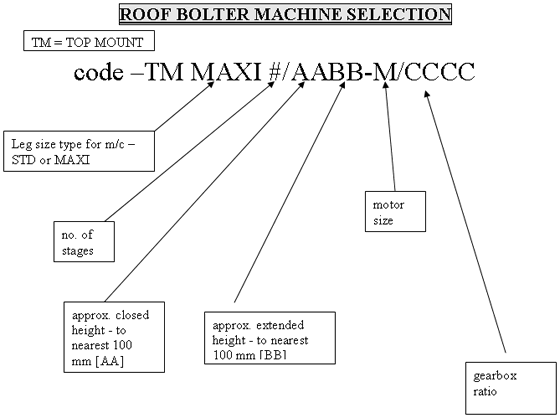
# = no. of stages: 3 or 4 or other on application
3 stage has outer plus 1st, 2nd and 3rd inner legs
4 stage has outer plus 1st, 2nd, 3rd and 4th inner legs
AABB = closed and extended lengths
e.g. 1023 - closed height is 1000mm; extended height is 2300mm
1332 - closed height is 1300mm; extended height is 3200mm
1746 - closed height is 1700mm; extended height is 4600mm
M =
Motor size: 70 or 95 70 = low torque motor
95 = suits low pressure supply, uses more air
note: normal air pressure is nominal 100psi [7 Bar], low air pressure nom.
70 psi [5 Bar]
CCCC =
gearbox ratio
1142 [11:42] = high torque/lower speed
1439 [14:39] = low torque/higher speed
NOTE: high torque motor is not available with high torque gearbox
A typical part description would be: R/B TM MAXI 3/1436-95/1439.
This indicates roof bolter, Top Mount, MAXI leg unit as compared to the standard leg version, 3 stage, closed height of 1400mm and extended of 3600mm (1436) [floor to top of chuck], 95mm air motor [other option is 70mm] and a 14:39 gearbox - this is our high speed unit compared to our high torque gearbox which has a 11:42 (1142) ratio.
The most popular styles of machines are MAXI, 3 stage and 95/1439 motor gearbox combination.